▏Product Vedio
▏Product Overview
In today’s modern manufacturing landscape, there is a growing demand for production automation, precise dosing, and efficient process control. The Plastic Material Dosing System is an indispensable device for companies striving to optimize production and enhance product quality. Integrating the functionalities of an Automatic formulation machine, a Small batch dosing machine, and an Ingredient dispensing machine, this high-end system is widely applied in the plastics, rubber, chemical, pharmaceutical, and food industries.
▏Key Features
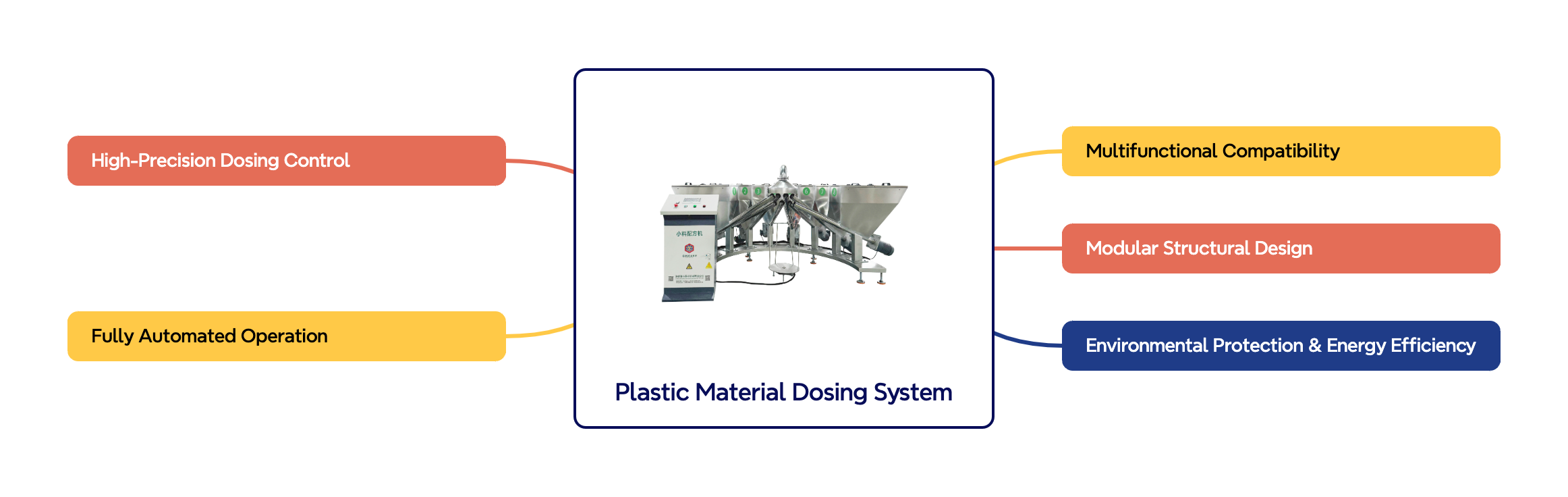
The Plastic Material Dosing System boasts numerous unique design elements and technical innovations that ensure high efficiency, stability, and accuracy even in demanding industrial environments.
 | High-Precision Dosing Control Ultra-Fine Precision: Utilizing advanced sensors and servo control systems, the device achieves dosing accuracies at the microgram or milligram level. Automatic Calibration: The system incorporates an automatic calibration module to maintain dosing accuracy over long-term operation. Intelligent Algorithms: Big data analytics and smart algorithms optimize material formulations, ensuring uniform mixing of ingredients. |
 | Fully Automated Operation
One-Touch Startup & Full Automation: The user-friendly interface minimizes the risk of manual errors with a simple one-touch operation. Real-Time Data Monitoring: Integrated with advanced PLC and SCADA systems, the device offers real-time monitoring of production parameters and automatic data logging. Self-Diagnostic & Fault Prevention: Built-in fault warning and self-diagnosis systems ensure any issues are flagged before affecting production, thus guaranteeing system stability. |
 | Multifunctional Compatibility
Automatic Formulation Machine: Supports automatic dosing and blending of various materials to meet diverse production requirements. Small Batch Dosing Machine: Ideal for trial production and sample development, enabling flexible small-batch manufacturing. Ingredient Dispensing Machine: Precisely controls the flow and ratio of different raw materials, ensuring consistency in formulations. |
 | Modular Structural Design
Modular Assembly: The system is constructed from multiple standard modules, facilitating easy disassembly, maintenance, and expansion. Highly Scalable: Customizable with various functional modules to suit specific customer needs. Excellent Compatibility: Seamlessly integrates with other automation equipment and production lines to form a comprehensive production system. |
 | Environmental Protection & Energy Efficiency
Low Energy Consumption: Incorporates advanced energy recovery systems and energy-saving motors to reduce power consumption. Eco-Friendly Materials: Constructed from environmentally friendly materials that meet international green standards. Low Noise Operation: Designed with noise reduction and sound insulation measures to create a comfortable working environment. |
Bullet List of Technical Parameters
 | Precision: ±0.1% Dosing Range: 0.1 grams to 100 kilograms Automatic Calibration Time: Under 30 seconds Control System: PLC + SCADA Operating Environment: Temperature range -10℃ to 50℃ |
Table of Key Characteristics
Feature | Description | Application Areas |
High-Precision Dosing | Microgram-level accuracy ensures perfect mixes | Pharmaceuticals, chemicals, plastics |
Automatic Calibration | Automatically corrects dosing errors | Continuous production |
Fully Automated Operation | One-touch startup and full automation | High-volume, automated factories |
Modular Structure | Easy maintenance and scalability | Customized production and upgrades |
Energy-Efficient & Eco-Friendly | Low energy consumption and noise reduction | Green manufacturing facilities |
▏Product Photo
▏Applications
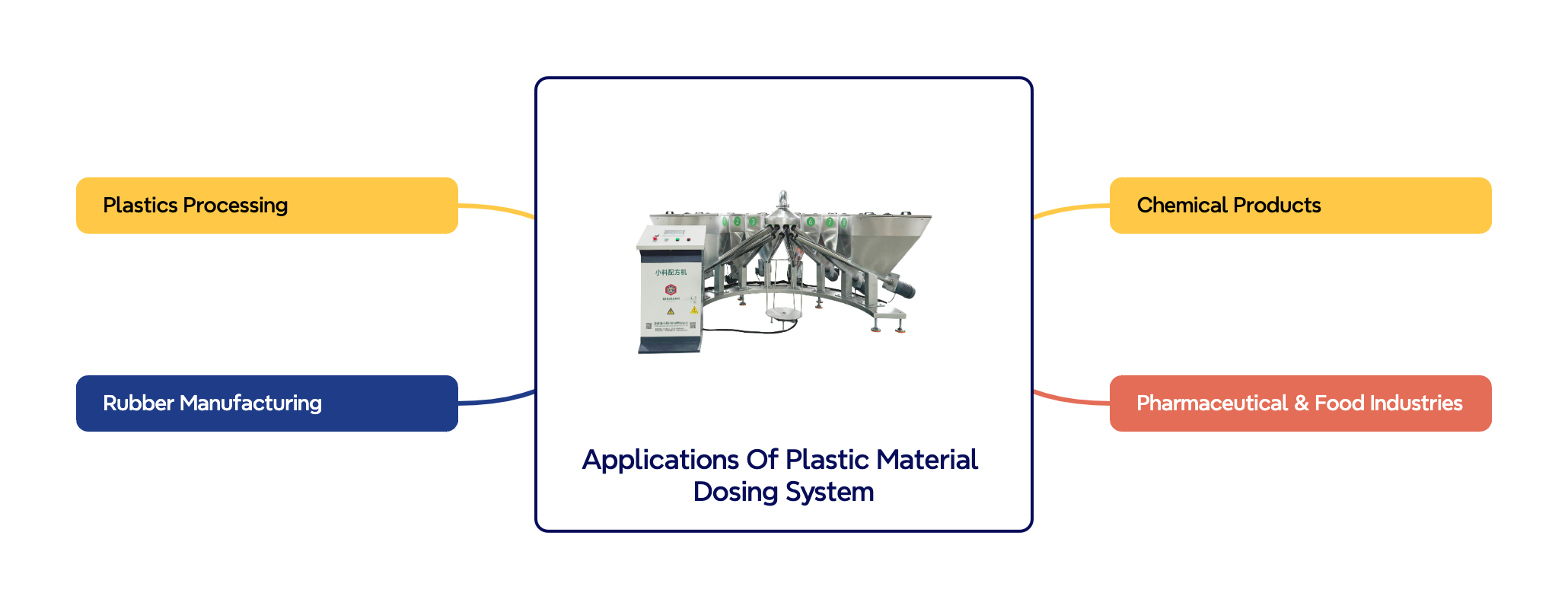
The Plastic Material Dosing System is widely employed across various industries. Its precise dosing and automated operation make it a key asset in enhancing production quality and efficiency.
 | Plastics Processing Injection Molding: Guarantees the accurate mixing of multi-component raw materials for high-quality injection molded parts. Extrusion Lines: Precisely controls the addition of various additives to optimize physical properties. Blow Molding: Ensures material consistency, resulting in improved overall product quality. |
 | Rubber Manufacturing Formula Mixing: Automatically mixes various rubbers and fillers for the production of high-performance rubber products. Pre-Vulcanization Dosing: Precisely adds vulcanizing agents and accelerators to enhance rubber properties. |
 | Chemical Products Precision Chemical Formulation: Ideal for producing coatings, adhesives, and other chemical products through exact dosing. Polymer Blending: Ensures fine control over raw materials during polymer synthesis, resulting in consistent formulations. |
 | Pharmaceutical & Food Industries Pharmaceutical Production: Precisely manages the ratio of active ingredients and excipients to guarantee product quality. Food Additives Blending: Ensures balanced mixtures of food additives, enhancing taste and nutritional value. |
Application Flowchart
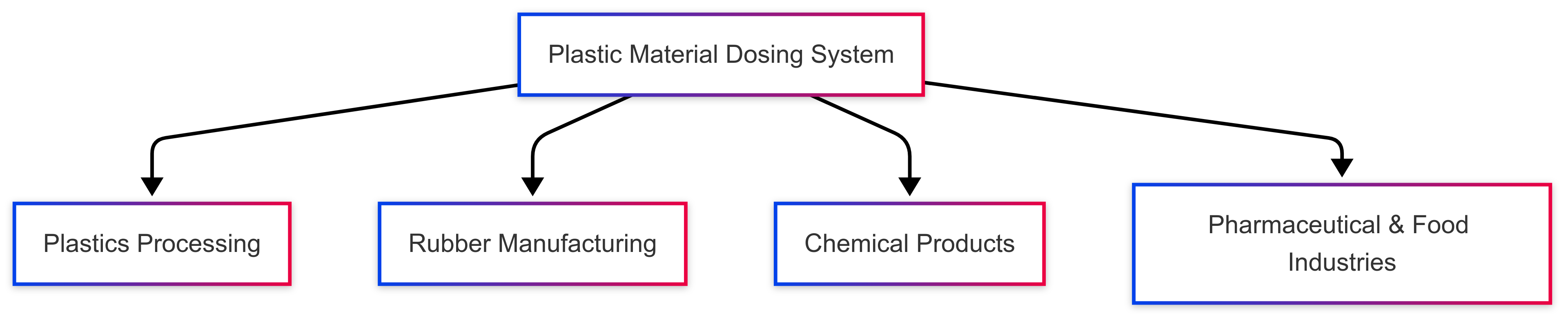
The above diagram clearly illustrates how the system plays a pivotal role across various sectors by leveraging its high precision, full automation, and modular design to significantly enhance production efficiency and product quality.
▏Advantages
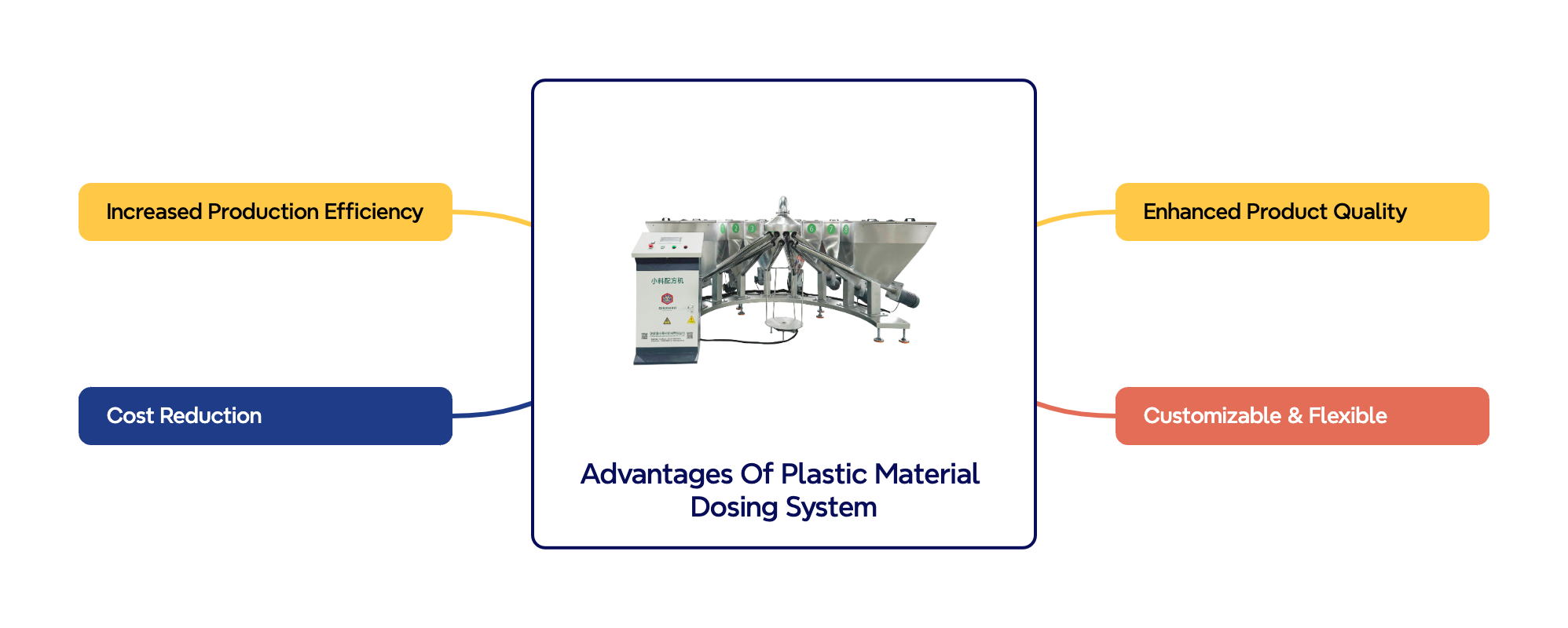
In today’s competitive market, the Plastic Material Dosing System stands out due to its technological leadership and highly efficient operational mode. Its advantages include:
 | Increased Production Efficiency Automated Operation: Reduces manual intervention and minimizes human error. Rapid Response: Real-time dosing and adjustment shorten the production cycle. Flexible Batching: Supports both small-batch trials and large-scale continuous production to meet diverse market needs. |
 | Cost Reduction Minimized Waste: Precise dosing eliminates raw material wastage and formulation errors. Energy Saving: Low power consumption and energy recovery systems significantly lower operational costs. Low Maintenance: Modular design simplifies maintenance, reducing overall upkeep expenses. |
 | Enhanced Product Quality Stable Formulation: Ensures uniform mixing and consistent product quality. High Reliability: Automatic calibration and fault diagnostics lower failure rates and maintain stable production. Traceability: Complete data logging allows for easy tracing of quality issues and process improvements. |
 | Customizable & Flexible Diverse Configurations: Customizable modules allow personalized system configurations. Robust Technical Support: Comprehensive technical consultations and after-sales support meet multi-layered customer needs. |
Advantages in a Bullet List
 | High level of automation with simple operation. Precise dosing ensures accurate formulations. Modular design enables easy expansion and maintenance. Energy-efficient and environmentally friendly. Real-time monitoring and self-diagnosis enhance production safety. |
▏System Configuration
The Plastic Material Dosing System is designed based on advanced industrial design principles. Its overall configuration comprises several interlinked modules that collectively form a complete automated production system.
Main Components
 | Dosing Module |
 | Control Module |
 | Conveying Module |
 | Mixing Module |
 | Safety & Environmental Module Incorporates overload protection, temperature safeguards, and noise reduction systems. Designed with energy-saving motors and meets international green standards. |
Configuration Table
Module | Main Functions | Key Technical Parameters | Remarks |
Dosing Module | Accurate measurement of raw materials | Precision: ±0.1% | Includes automatic calibration |
Control Module | Real-time monitoring and automatic control | PLC & SCADA system | Remote operation enabled |
Conveying Module | Smooth transport of materials | Screw conveyor, vibration feeder | Blockage detection system |
Mixing Module | Uniform blending of ingredients | Multi-stage mixer, adjustable speed | Suitable for diverse formulas |
Safety Module | Equipment protection and energy saving | Overload, temperature controls | Complies with green standards |
▏Production Process
To ensure every batch meets stringent quality standards, the Plastic Material Dosing System follows a standardized production process with rigorous quality control measures at every stage.
 | Raw Material Reception & Pre-Treatment Material Inspection: Incoming raw materials undergo visual, compositional, and quality inspection to ensure compliance with production standards. Pre-Treatment: Materials are pre-treated (drying, filtering, pre-mixing) to ensure stable dosing performance. |
 | Precise Dosing Automatic Feeding: The dosing module automatically feeds raw materials based on pre-set formulas, using high-precision sensors. Automatic Calibration: Built-in calibration routines correct any initial dosing discrepancies to maintain accuracy within allowable limits. |
 | Mixing & Blending Stepwise Mixing: Materials are progressively mixed using the multi-stage mixer, ensuring each component is uniformly integrated. Dynamic Monitoring: Real-time monitoring systems track all mixing parameters to guarantee uniformity and consistency. |
 | Discharge & Packaging Controlled Discharge: The mixed product is uniformly discharged via the automated conveying system, ensuring consistent product quality. Packaging & Inspection: Final products are automatically inspected and packaged after a rigorous quality check. |
Production Flowchart

This flowchart outlines the entire production process from raw material reception to final packaging, ensuring that every step is precisely controlled and monitored for optimal product quality.
▏Customer Case Studies
Our Plastic Material Dosing System has been successfully implemented by numerous renowned companies across various industries. Here are a few notable customer case studies:
 | Case Study 1: International Plastics Manufacturer Background: The company produces high-precision plastic products and demanded absolute accuracy in formulations. Solution: Our automatic formulation machine was deployed to achieve precise dosing and dynamic calibration, leading to improved production efficiency and higher product quality. Results: Dosing accuracy was maintained within ±0.1%, production cycle reduced by 20%, and customer satisfaction was greatly enhanced. |
 | Case Study 2: Major Rubber Products Manufacturer
Background: Facing challenges with manual dosing inaccuracies in rubber production. Solution: Implementation of our small batch dosing machine ensured accurate raw material distribution and consistent mixing. Results: Achieved a 30% reduction in waste and significant improvements in product consistency, resulting in lower production costs. |
 | Case Study 3: Chemical Coatings Producer
Background: Required precise control over multiple chemical components for high-quality coatings. Solution: Our ingredient dispensing machine technology was integrated to ensure each component was accurately dosed. Results: Enhanced mixing uniformity, increased production efficiency, and notable energy savings. |
▏Why Choose Us
Choosing our Plastic Material Dosing System means opting for a comprehensive solution that blends advanced technology, unmatched service, and significant economic benefits. Here’s why we stand out:
 | Strong Technical Expertise
Expert R&D Team: Our experienced team consistently incorporates cutting-edge international technology. Continuous Innovation: We continually optimize product design to elevate automation and intelligence. Certifications & Patents: Multiple technologies have been patented and certified under ISO and CE standards. |
 | Customized Service
Tailor-Made Solutions: We design personalized dosing systems based on the client’s specific production needs. Flexible Configurations: Our modular design supports custom expansions and secondary developments. Professional Support: Comprehensive technical consultation, training, and remote assistance ensure seamless operation. |
 | Superior After-Sales Support
Rapid Response: Our 24/7 customer service guarantees timely problem resolution. Scheduled Maintenance: Regular maintenance, software upgrades, and technical inspections prolong equipment lifespan. Proven Track Record: Numerous successful implementations in leading companies demonstrate our reliability. |
 | Dual Benefits: Cost Efficiency & Enhanced Quality
Cost Reduction: High-precision dosing minimizes raw material wastage and reduces labor costs. Quality Enhancement: Stable and consistent formulations boost overall product quality. Eco-Friendly: Our energy-efficient and low-noise design supports sustainable production practices. |
Why Choose Us – A Summary List
 | Cutting-edge R&D and continuous innovation. Customized solutions and flexible configurations. Reliable, round-the-clock after-sales service. Verified performance through numerous industry success stories. Comprehensive cost and quality benefits. |
▏Additional Information
 | Frequently Asked Questions (FAQ) Q: Is the installation and commissioning process complicated? A: Thanks to the modular design and full technical support provided by our team, installation and commissioning are straightforward, ensuring a fast production ramp-up. Q: How does the system maintain long-term dosing precision? A: With built-in automatic calibration and intelligent algorithms, the system continually adjusts to ensure high-precision dosing over time. Q: Does the system support remote monitoring and data analysis? A: Absolutely. Our SCADA-based control system enables remote monitoring, real-time data acquisition, and comprehensive reporting. |
 | Technical Documentation Downloads
We offer detailed user manuals, installation guides, and maintenance handbooks for easy reference and operation support. |
 | Industry News & Technical Blog
Stay updated with the latest industry trends, technological advancements, and market analyses through our regularly updated blog. Our insights help you stay ahead in an increasingly competitive market. |
The Plastic Material Dosing System is a forward-thinking, high-precision automation device that integrates the functionalities of an Automatic formulation machine, a Small batch dosing machine, and an Ingredient dispensing machine. By combining precise dosing, full automation, modular design, and eco-friendly principles, our system is poised to revolutionize production in the plastics, rubber, chemical, pharmaceutical, and food industries. Whether you are engaged in large-scale continuous production or small-batch trials, our solution is designed to meet modern manufacturing demands for both precision and efficiency.
By choosing our system, you are investing in a technology-driven, cost-effective, and high-quality production solution. Our commitment to innovation, customer service, and sustainability makes us the ideal partner for businesses aiming to achieve excellence in manufacturing.
▏About Us
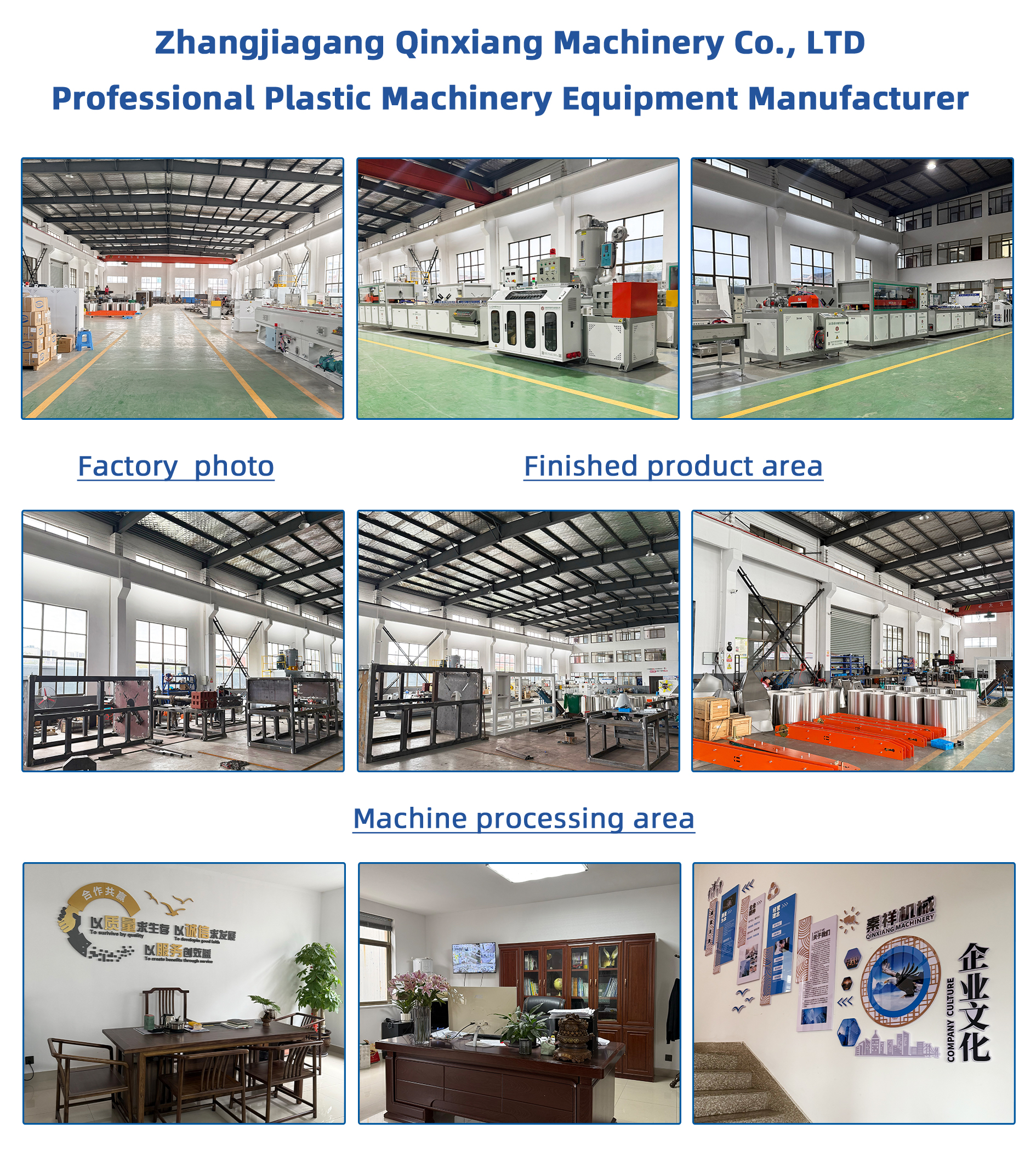
▏Corporate Culture
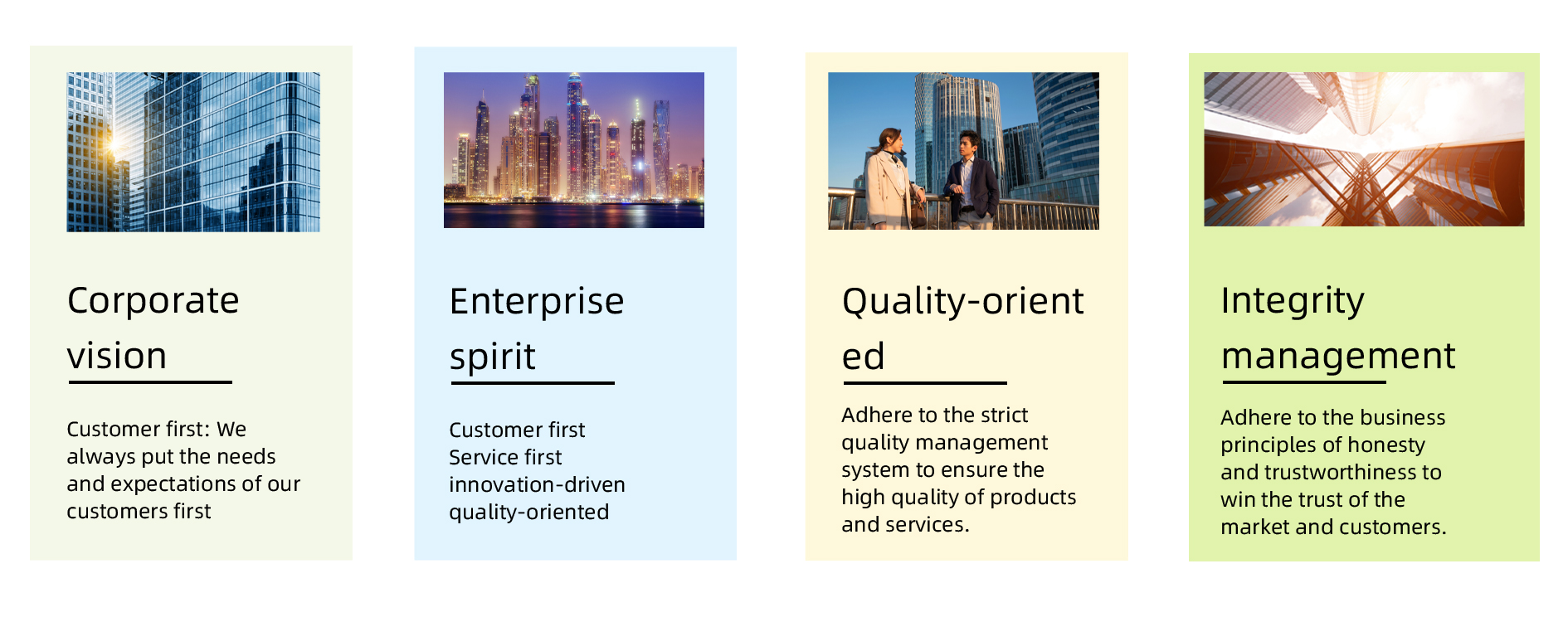
▏Cooperative Parts Supplier
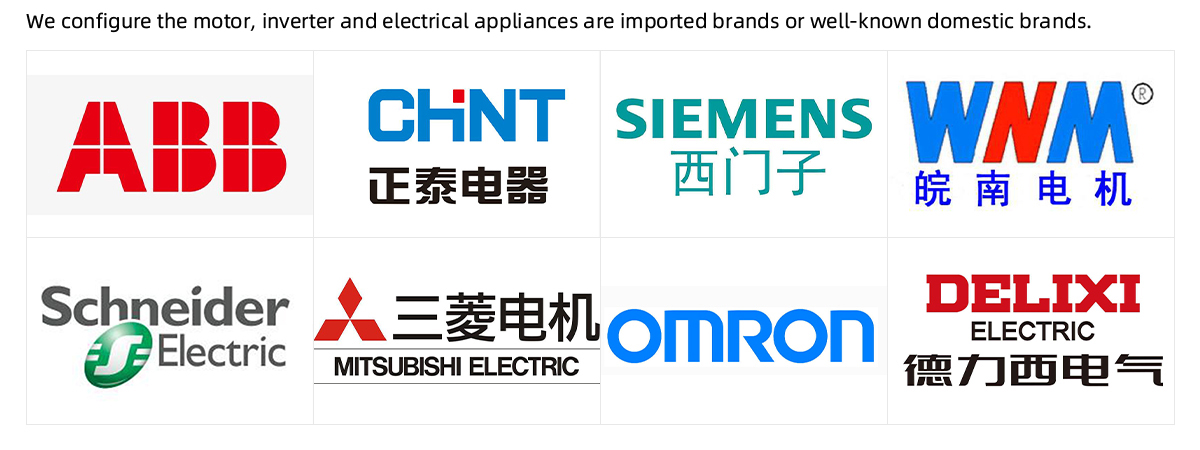
▏Packing And Shipping
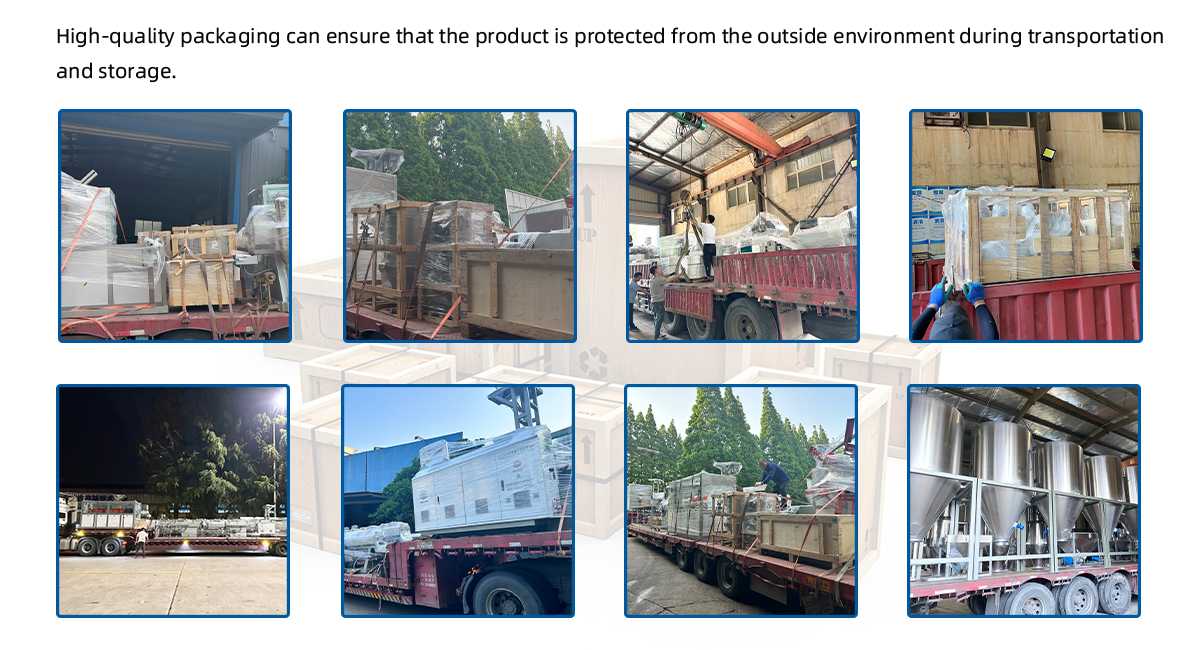