▏Product Vedio
▏Introduction
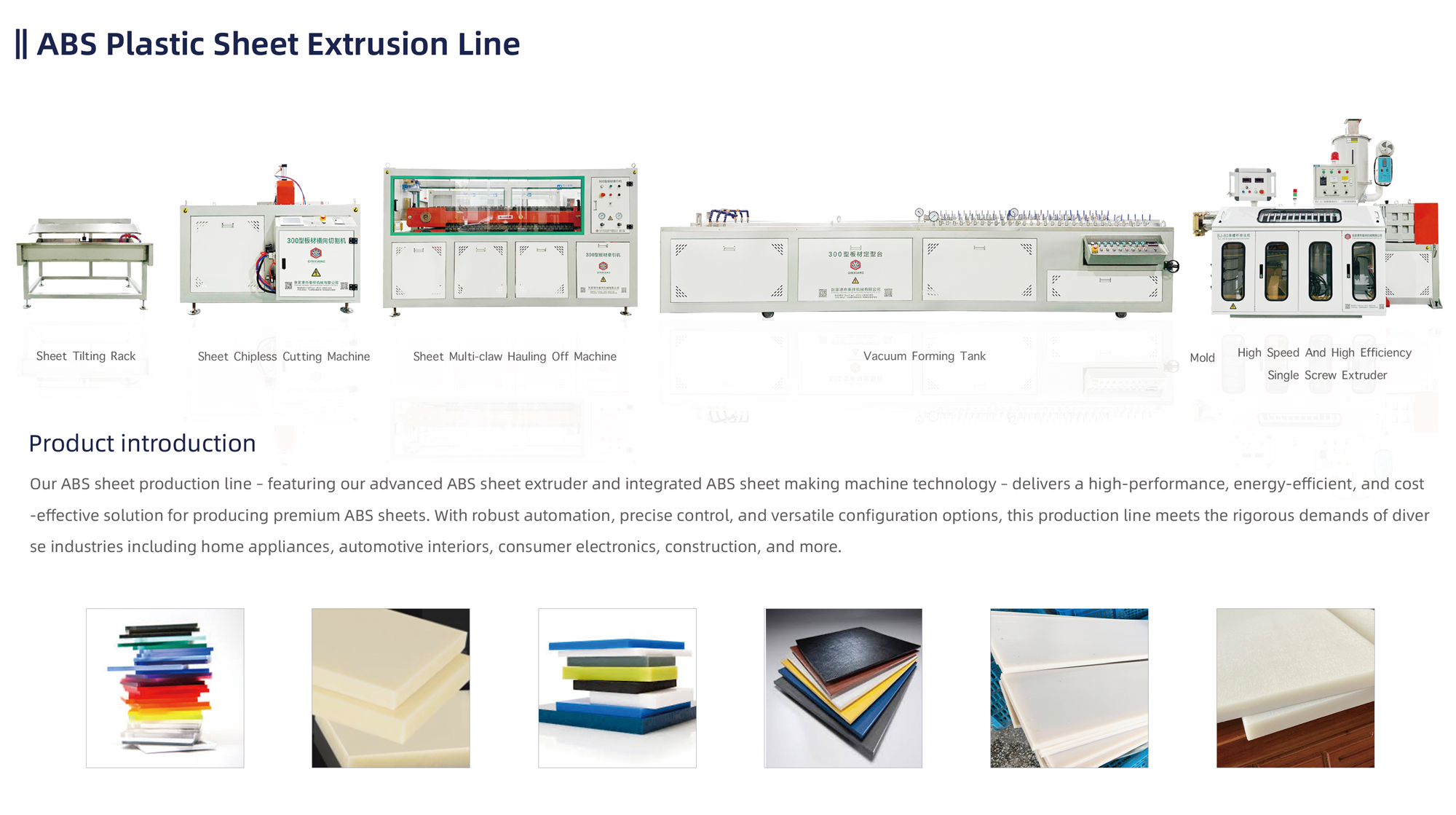
In today’s high-end plastics market, ABS (Acrylonitrile Butadiene Styrene) is highly favored for its excellent mechanical properties, impact resistance, and ease of processing. As an essential engineering plastic, ABS sheets are widely used in automotive interiors, household appliances, consumer electronics, architectural decoration, and packaging industries. To meet the growing market demand, an efficient, stable, and energy-saving ABS sheet production line is of paramount importance. Our ABS sheet production line is composed of an advanced ABS sheet extruder, automated process equipment, and an intelligent control system that integrates the latest technology to enable continuous, high-quality production of ABS sheets.
▏Main Features of the ABS Sheet Production Line
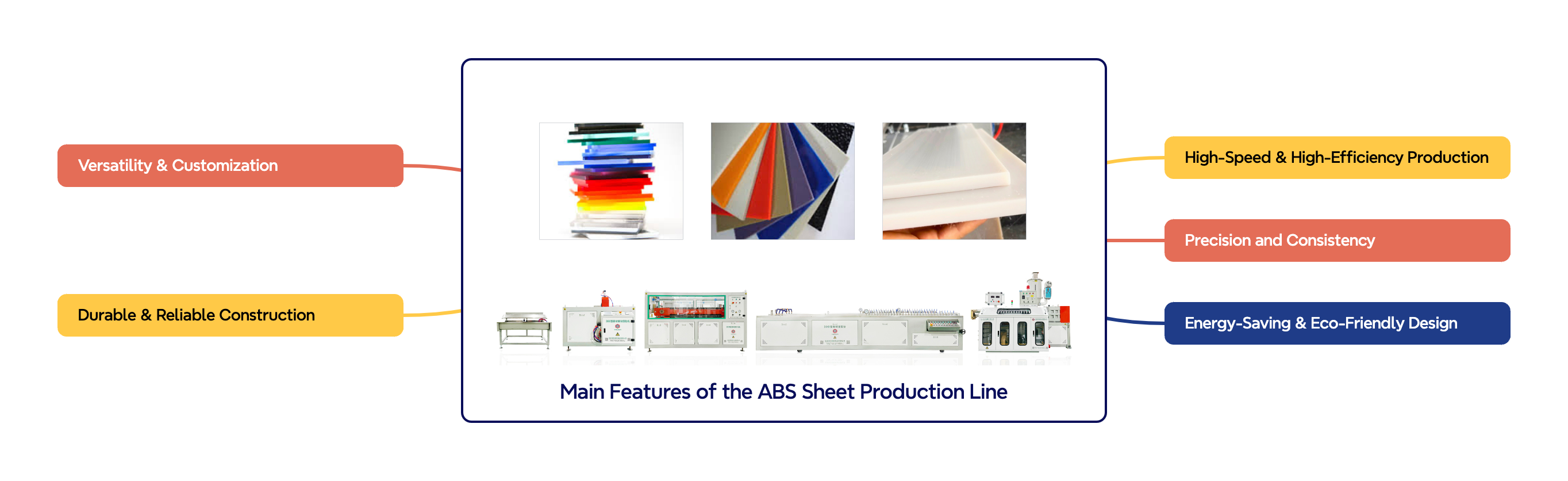
 | High-Speed & High-Efficiency Production Our advanced ABS sheet extruder is designed with cutting-edge technology to achieve high-speed production rates of hundreds of kilograms per hour. The optimized screw and barrel configuration ensures efficient plasticization and consistent output, maintaining uniform sheet thickness and surface quality even under high-speed operation. Precision die and modular design facilitate quick changeovers and high production stability. |
 | Precision and Consistency
An automated PLC touchscreen control system continuously monitors critical parameters such as temperature, pressure, and flow, ensuring each sheet meets quality standards. Real-time data acquisition and remote monitoring guarantee consistent product dimensions and minimize defects. Advanced mixing and homogenization processes eliminate material segregation, resulting in superior sheet quality. |
 | Energy-Saving & Eco-Friendly Design
Intelligent temperature control combined with an efficient cooling system significantly reduces energy consumption, meeting international energy-saving standards. Optimized process design minimizes material waste and scrap, improving overall resource utilization. The production line supports the use of recycled ABS, promoting sustainable and eco-friendly manufacturing practices. |
 | Versatility & Customization
The production line supports single-layer, multi-layer co-extrusion, and composite sheet production, catering to diverse market demands. It can produce ABS sheets in various widths, thicknesses, and surface finishes (high-gloss, matte, textured, etc.). Modular configuration allows for flexible upgrades and scalability to suit different production scales and custom requirements. |
 | Durable & Reliable Construction
Built with high-strength stainless steel and premium alloys, the production line is engineered for long-term operation even under high load. Key components undergo rigorous anti-corrosion and wear tests, ensuring excellent durability and extended service life. The low-noise, low-vibration design creates a comfortable working environment in the production facility. |
▏Product Photo
▏Customer Case
▏Applications of the ABS Sheet Production Line
Our ABS sheet production line is versatile and finds applications across a variety of industries, including:
 | Automotive Industry Household Appliances Consumer Electronics Casings for televisions, monitors, printers, mobile phones, and laptops. Architectural Decoration Packaging Industrial Applications |
This production line can be easily adjusted to produce customized ABS sheets that meet the specific requirements of various sectors, ensuring versatility and market adaptability.
▏Advantages of Our ABS Sheet Production Line
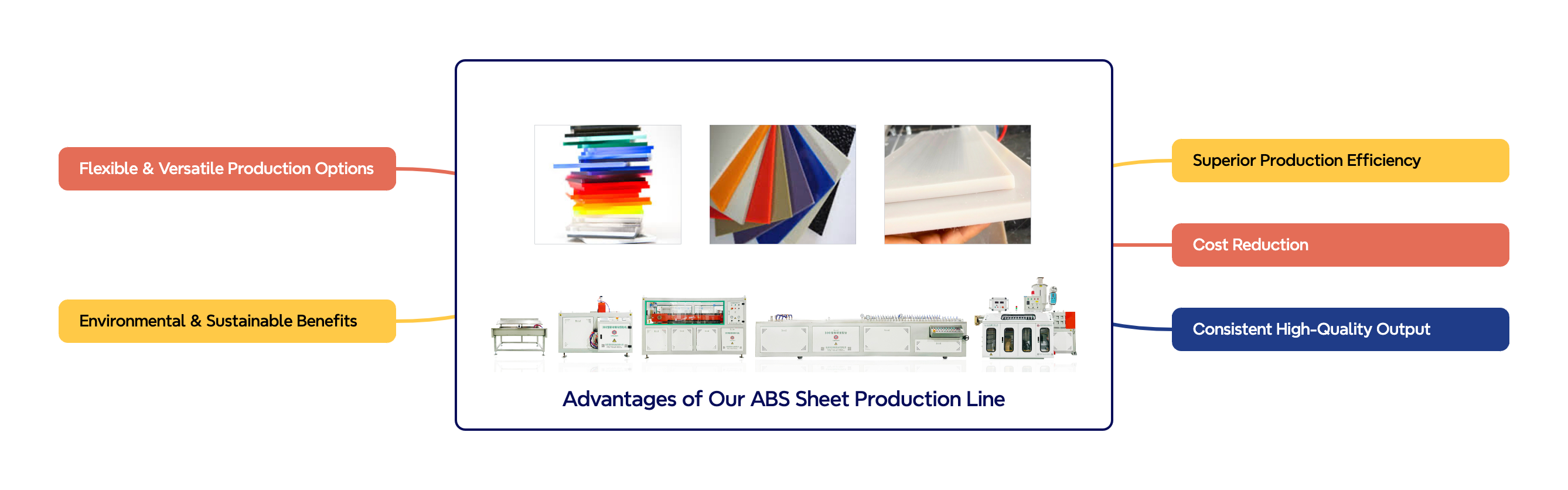
 | Superior Production Efficiency
High-speed continuous production: Advanced extruder technology and automated systems significantly reduce production cycle times. Stable product quality: Automated monitoring and precise control ensure that each batch of ABS sheets meets the stringent quality standards. |
 | Cost Reduction
Energy optimization: Intelligent heating and cooling systems minimize energy usage, lowering operating costs. High material utilization: Precise control minimizes waste and scrap, reducing overall production costs. |
 | Consistent High-Quality Output
Precision control: Strict control of process parameters guarantees uniform thickness, surface finish, and mechanical properties. Advanced detection systems: Online quality inspection systems ensure that only sheets meeting quality criteria continue in the production process. |
 | Flexible & Versatile Production Options
Customization: Easily configurable to produce ABS sheets with various sizes, thicknesses, and textures tailored to customer demands. Modular design: Quick installation, maintenance, and scalability allow the production line to adapt to evolving market trends. |
 | Environmental & Sustainable Benefits
Green manufacturing: Designed to meet international environmental standards and support the use of recycled ABS materials. Reduced emissions: Energy-efficient technology contributes to lower carbon emissions, aligning with global sustainability initiatives. |
▏Configuration of the ABS Sheet Production Line
Below is a sample configuration for our ABS sheet production line. Customization options are available to suit various production scales and customer specifications:
Configuration Item | Details |
Main Extruder | High-performance ABS sheet extruder (ABS sheet extruder) |
Extrusion Die | Customizable flat die for uniform sheet formation |
Cooling System | Multi-stage water and air cooling system for rapid sheet solidification |
Haul-Off System | Servo-controlled high-speed traction system ensuring uniform stretching |
Cutting Unit | Planetary cutter with automatic length detection for precise cutting |
Quality Inspection | Online measurement system for thickness, width, and surface quality |
Packaging Unit | Automated stacking, coiling, and bundling system for efficient handling |
Auxiliary Equipment | Automatic feeding system, exhaust and air handling, smart control system |
In addition to the standard configuration, we offer tailored solutions and additional modules to meet specific customer requirements.
▏ABS Sheet Production Process
Process Flow Diagram
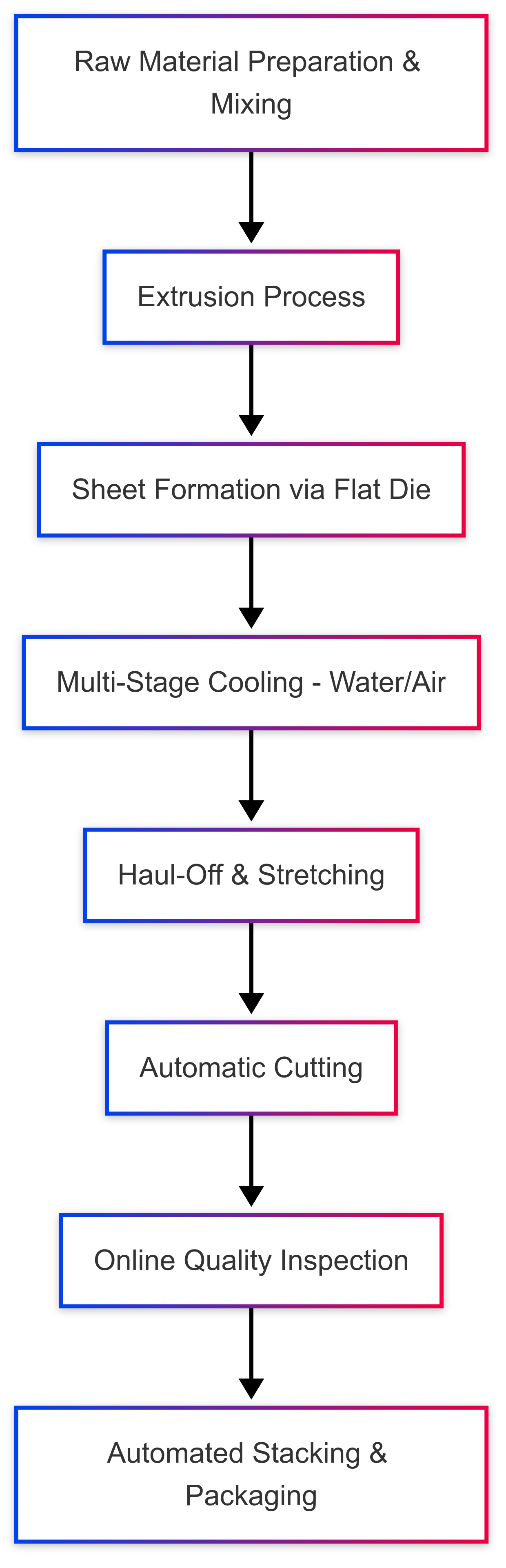
Detailed Process Steps
 | Raw Material Preparation & Mixing ABS resin is blended with stabilizers, pigments, and other additives in precise ratios. An automatic feeding system ensures a constant, homogeneous supply of raw materials to the extruder. |
 | Extrusion Process The pre-mixed ABS material is fed into the ABS sheet extruder, where it is heated, melted, and homogenized by the twin-screw system. The extruder precisely controls temperature and pressure to achieve optimal plasticization. |
 | Sheet Formation via Flat Die |
 | Multi-Stage Cooling (Water/Air) The hot sheet is passed through a series of cooling rollers and water/air cooling systems to rapidly solidify the material. Controlled cooling minimizes internal stresses and maintains the sheet’s dimensional stability. |
 | Haul-Off & Stretching A servo-controlled haul-off system pulls the cooled sheet at a consistent speed, ensuring uniform stretching and preventing deformation. Real-time tension monitoring ensures optimal sheet quality. |
 | Automatic Cutting |
 | Online Quality Inspection High-precision sensors and cameras conduct real-time quality checks for thickness, width, surface finish, and overall integrity. Data from inspections is fed back into the control system for continuous process optimization. |
 | Automated Stacking & Packaging Approved sheets are automatically coiled, stacked, and packaged for efficient storage and transportation. The packaging system minimizes manual handling, reducing labor costs and increasing overall productivity. |
▏Customer Case Studies
 | Case Study 1: American Home Appliance Manufacturer
Background: An American home appliance manufacturer required high-quality ABS sheets for refrigerator panels and washing machine covers. Their previous production system struggled to meet both the quality and production volume requirements. Results: Production capacity increased by 45% due to the advanced ABS sheet production line. Achieved a significant reduction in material waste and energy consumption. Consistent high-quality ABS sheets led to enhanced product performance and customer satisfaction. |
 | Case Study 2: European Automotive Interior Supplier
Background: A European supplier specializing in automotive interior components needed ABS sheets with superior surface finish and dimensional accuracy for dashboard and door panel production. Results: Defect rate reduced by 25% following the upgrade to our ABS sheet extruder. Enhanced control over sheet thickness and surface quality led to higher product reliability. The system’s flexibility enabled rapid adjustments to meet changing design requirements. |
 | Case Study 3: Asian Consumer Electronics Company
Background: A leading consumer electronics company in Asia sought a reliable ABS sheet making machine for producing casings for laptops and printers, requiring vibrant colors and high gloss finishes. Results: Improved sheet quality with uniform texture and color consistency. Overall production cost reduced by 20% through optimized process control and energy efficiency. The company successfully expanded into new markets with high-end product offerings. |
▏Why Choose Us
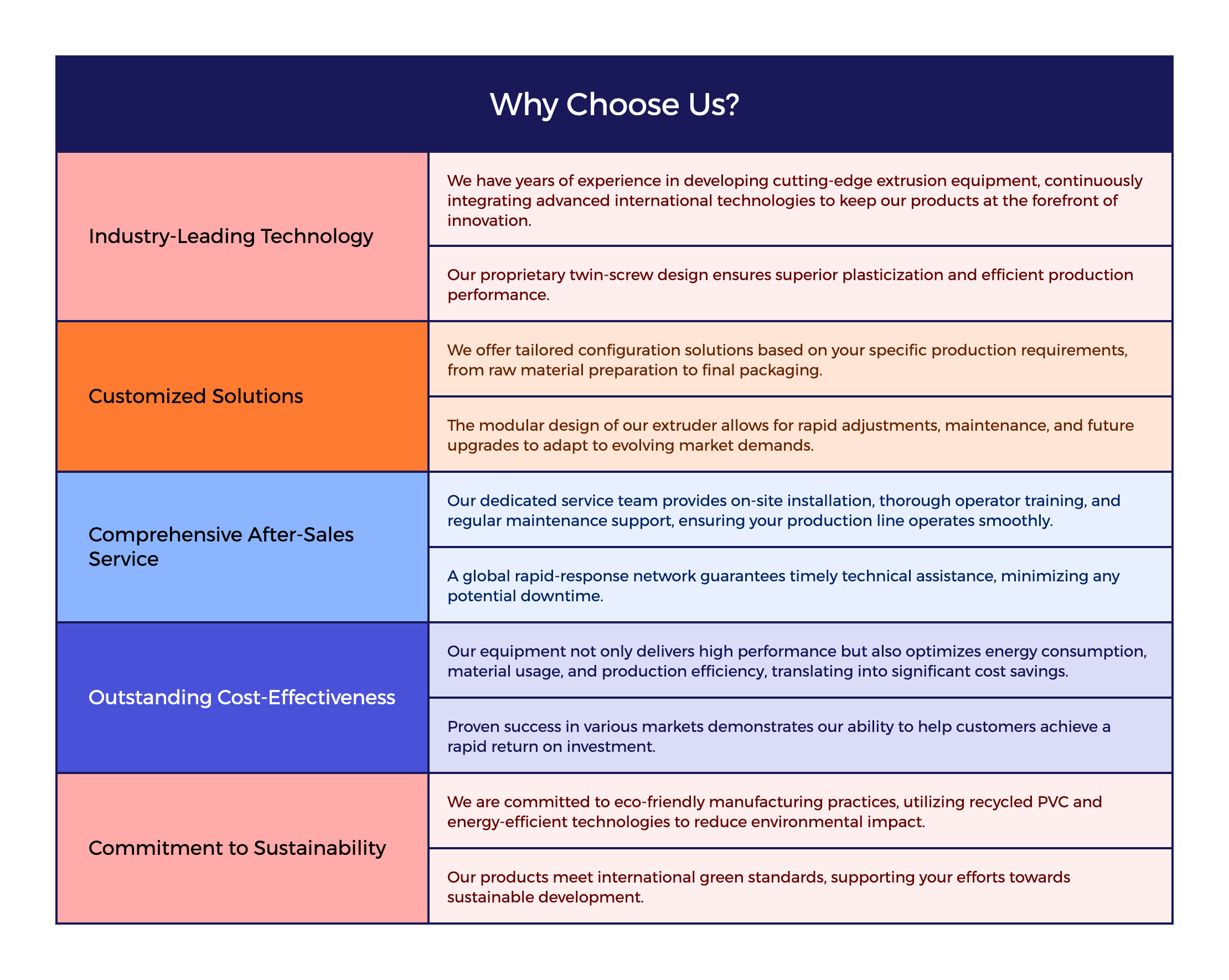
 | Industry-Leading Technology
Our ABS sheet production line leverages state-of-the-art extrusion technology and smart control systems, ensuring superior product quality and high efficiency. Continuous innovation and rigorous quality control keep our products at the forefront of industry standards. |
 | Tailor-Made Solutions
We offer customized production line configurations designed to meet the unique needs of various industries. Our modular design enables rapid setup, easy upgrades, and scalable production capacity. |
 | Comprehensive After-Sales Support
Our dedicated service team provides on-site installation, thorough operator training, and ongoing maintenance support to ensure uninterrupted production. With a global network of service centers, we guarantee prompt response and resolution of any issues. |
 | Exceptional Cost-Effectiveness
|
 | Commitment to Sustainability
Our production line is designed with environmental responsibility in mind, supporting green manufacturing and the use of recycled ABS. We help our customers meet international environmental standards while reducing their carbon footprint. |
In summary, our ABS sheet production line – featuring our advanced ABS sheet extruder and integrated ABS sheet making machine technology – delivers a high-performance, energy-efficient, and cost-effective solution for producing premium ABS sheets. With robust automation, precise control, and versatile configuration options, this production line meets the rigorous demands of diverse industries including home appliances, automotive interiors, consumer electronics, construction, and more.
Our comprehensive solution ensures consistent product quality, enhanced production efficiency, and significant cost savings, making it the ideal choice for businesses looking to upgrade their manufacturing capabilities. If you are seeking a reliable and customizable ABS sheet production line that aligns with modern environmental standards and maximizes ROI, look no further.
Contact us today to learn more about our tailored solutions, technical specifications, and after-sales support. Let us help you elevate your production process and gain a competitive edge in the global marketplace!
▏About Us
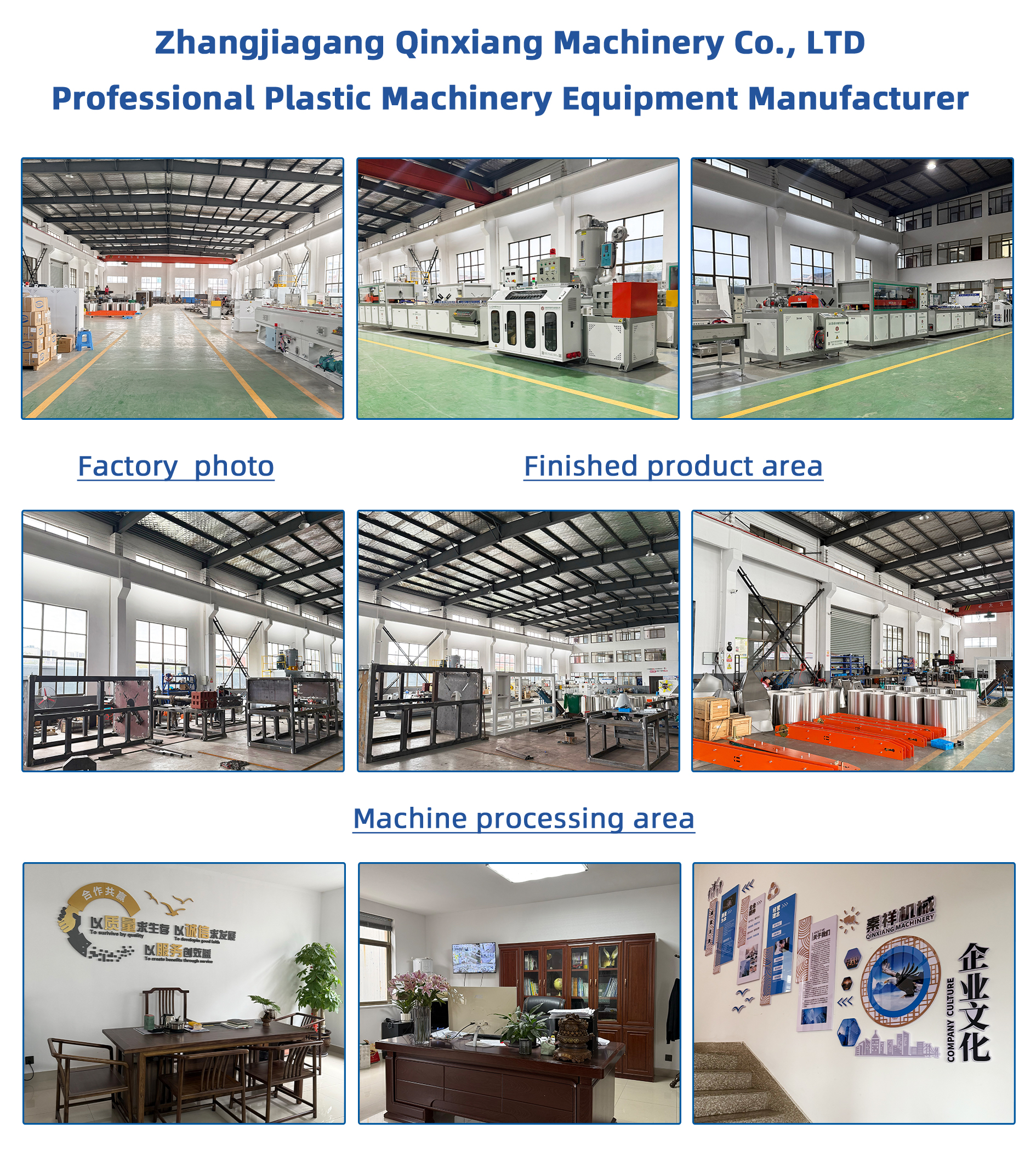
▏Corporate Culture
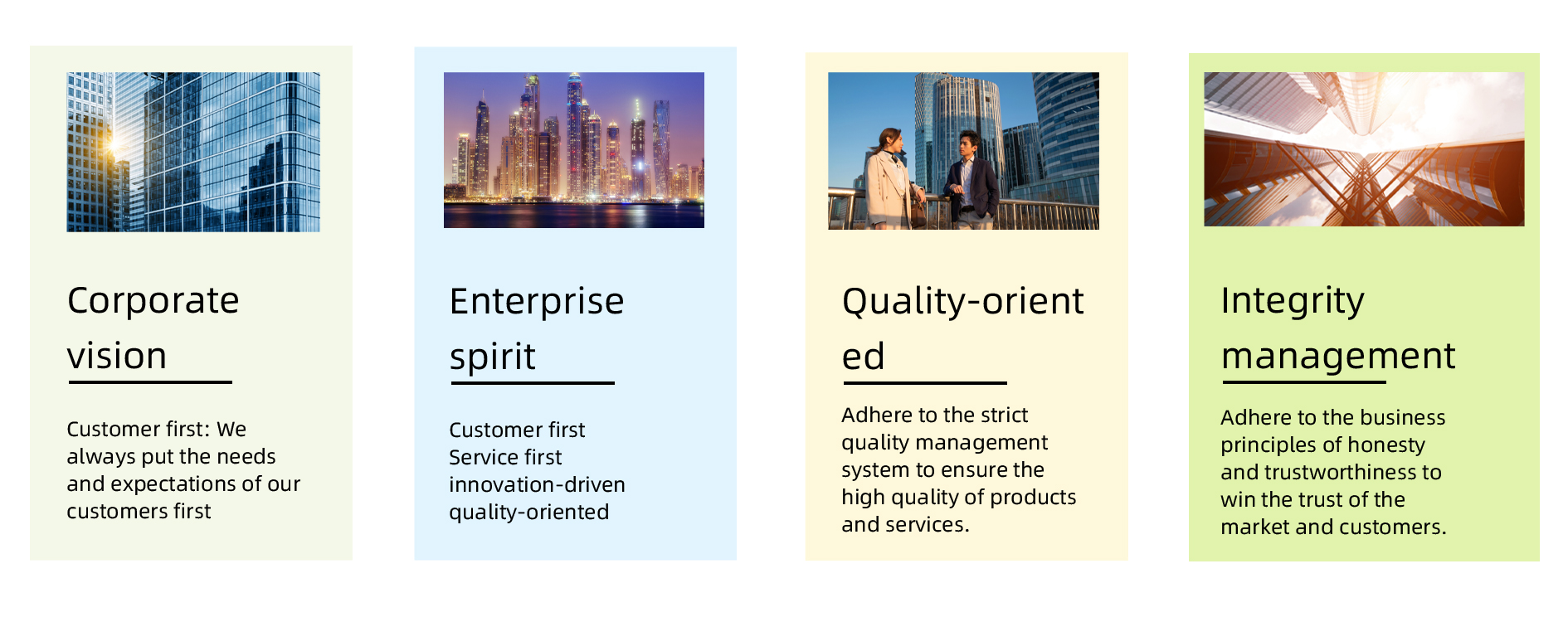
▏Cooperative Parts Supplier
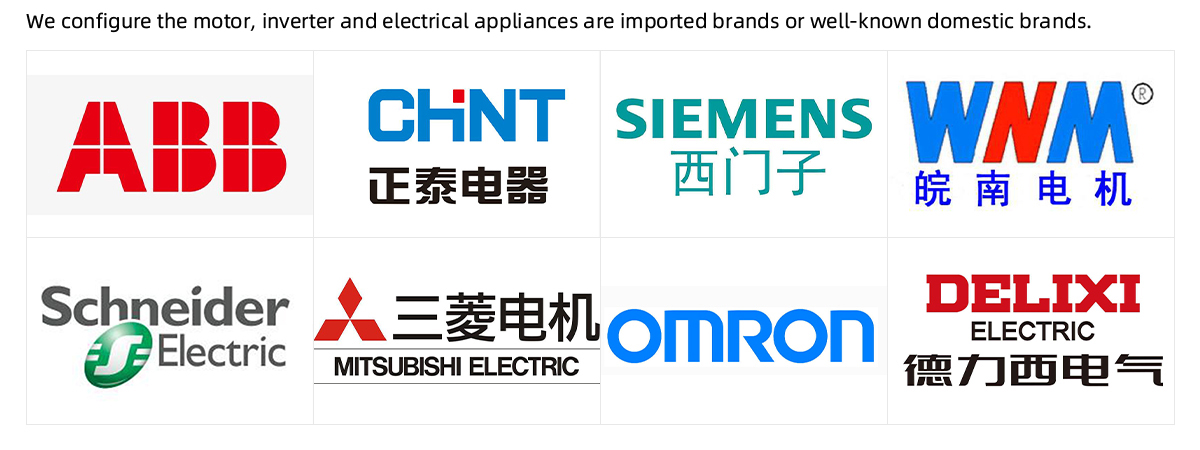
▏Packing And Shipping
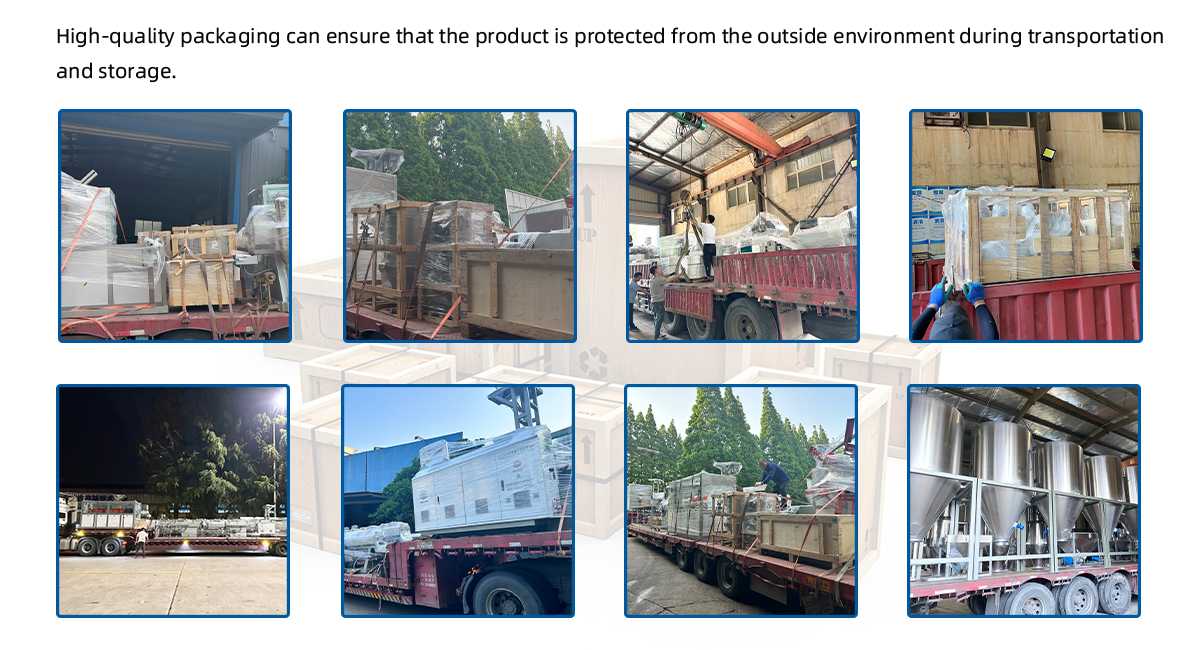