▏Product Vedio
▏Product Introduction
In the field of research and development and experiment, accurate and reliable small extrusion equipment is of vital significance for the development of new materials, process optimization and product trial production. The experimental extruder is designed for research and development experiments and small series production, enabling efficient mixing, melting, extrusion and molding of materials in a laboratory environment. Whether used for material performance testing, process parameter verification, or new product prototype development, experimental extruders can provide a reliable technical support and data foundation for enterprises.
▏Key Features of the Small-scale extruder
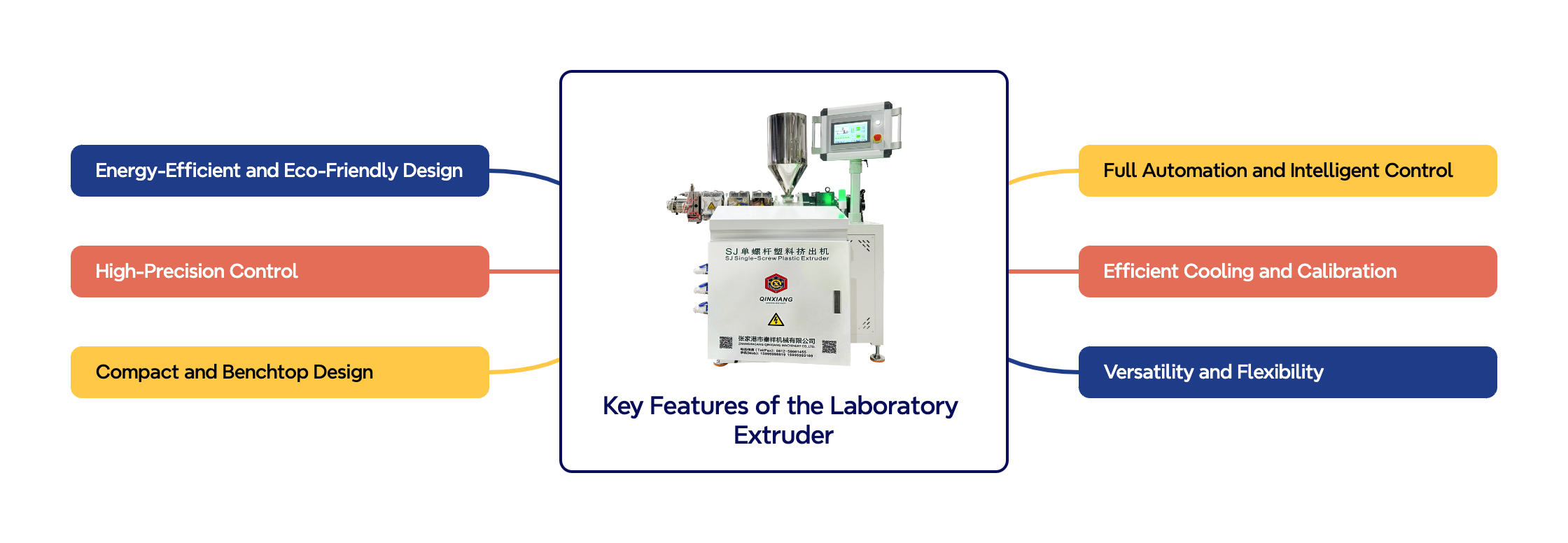
 | High-Precision Control
Accurate Temperature Control: Our Small-scale extruder features a multi-zone heating system with high-precision sensors, ensuring uniform melt temperature throughout the extrusion process. Precise Flow Regulation: The digital control system allows for exact adjustment of material flow and screw speed, meeting the demands of small-batch experiments. |
 | Compact and Benchtop Design
Small-Scale & Portable: Designed as a benchtop extruder, it occupies minimal space and is ideal for laboratory environments and research centers. Modular Construction: A modular design facilitates easy disassembly, maintenance, and upgrades, reducing downtime and maintenance costs. |
 | Full Automation and Intelligent Control
PLC Touchscreen Interface: The fully automated system provides intuitive control over all process parameters, from material pre-treatment to final extrusion. Real-Time Data Acquisition: Online monitoring collects real-time data on temperature, pressure, and screw speed, enabling immediate adjustments to ensure consistency. |
 | Efficient Cooling and Calibration
Multi-Stage Cooling: The extruded material passes through a series of water and air cooling stages, ensuring rapid, uniform solidification and minimal thermal deformation. Precision Calibration: Calibration modules adjust cooling parameters in real time to maintain consistent thickness. |
 | Versatility and Flexibility
Multi-Functionality: Capable of single-layer, dual-layer, and multi-layer co-extrusion, the machine is adaptable to various research needs. Material Compatibility: Suitable for processing a wide range of thermoplastics, making it ideal for diverse R&D applications. |
 | Energy-Efficient and Eco-Friendly Design
|
▏Product Photo
▏Customer Case
▏Applications of the Small-scale extruder
Our Small-scale extruder is widely used in various R&D and pilot production scenarios, including:
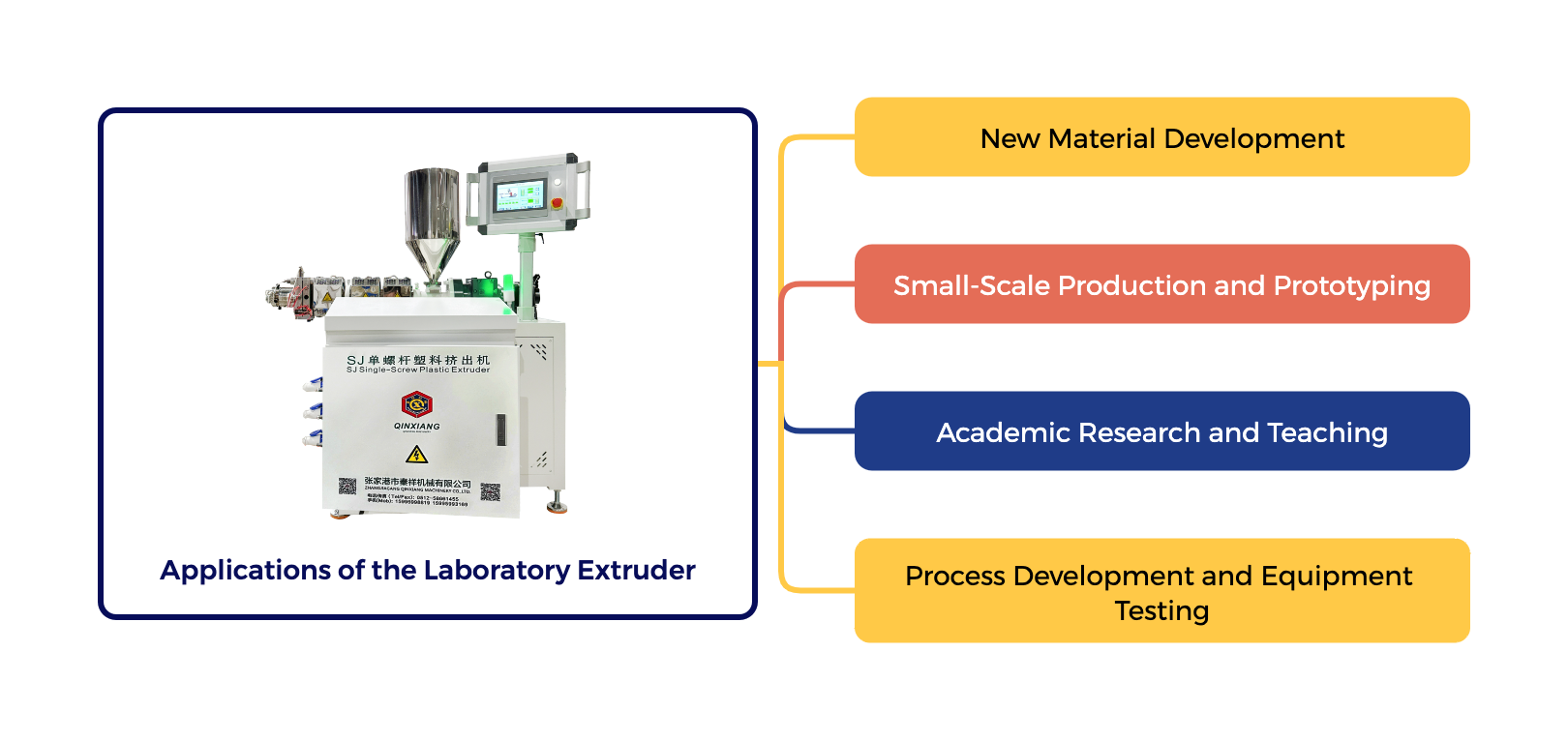
 | New Material Development
Formulation Testing: Researchers can test new material formulations, evaluating processing behavior and end-product performance. Process Optimization: Fine-tune processing parameters such as temperature, pressure, and screw speed to optimize material properties before full-scale production. |
 | Small-Scale Production and Prototyping
Prototype Manufacturing: Quickly produce prototypes and small batches for market testing and concept validation. Custom Pilot Runs: Ideal for startups and research institutions requiring low-volume, high-precision production. |
 | Academic Research and Teaching
Research Experiments: Universities and research labs use the extruder for experiments in material science, polymer processing, and mechanical engineering. Educational Demonstrations: Provides hands-on experience in extrusion technology for students in engineering and materials courses. |
 | Process Development and Equipment Testing
Process Innovation: Test and refine new processing techniques and equipment modifications in a controlled, small-scale setting. Pre-Production Trials: Validate production processes before scaling up to full production lines. |
▏Advantages of Our Small-scale extruder
 | Cost-Effective for R&D
Lower Investment: Small-scale extruders require a lower capital investment, making them ideal for research institutions and startups. Reduced Operating Costs: Energy-efficient design and automated processes reduce operational expenses. |
 | Ease of Use
User-Friendly Interface: The intuitive touchscreen interface allows even non-expert operators to quickly learn and operate the machine. Simple Maintenance: Modular design ensures easy access to key components, reducing maintenance time and costs. |
 | High Precision and Stability
Consistent Output: Advanced temperature and flow control maintain consistent material properties and thickness, meeting ±0.05mm tolerance requirements. Reliable Data Collection: Real-time monitoring and automated adjustments ensure experimental data is accurate and repeatable. |
 | Flexibility in Applications
Versatile Material Processing: Capable of processing various thermoplastics, it supports a wide range of R&D projects. Customizable Configuration: Easily adjustable parameters allow for rapid switching between different experimental setups. |
 | Environmental Benefits
|
▏Configuration of the Small-scale extruder
Below is a typical configuration for our Small-scale extruder, which can be customized to meet specific research needs:
Configuration Item | Details |
Main Unit | Laboratory extruder (Small-scale extruder/Benchtop extruder/Mini extruder machine) |
Screw System | High-precision twin-screw system ensuring uniform mixing and extrusion |
Temperature Control | Multi-zone heating system with high-precision sensors |
Cooling System | Multi-stage water and air cooling system for rapid, uniform solidification |
Control Interface | PLC touchscreen control panel with real-time data acquisition |
Material Feeding System | Automatic feeding unit ensuring continuous, homogeneous material supply |
Safety System | Over-temperature, over-pressure sensors and alarms |
Auxiliary Modules | Customizable dies, calibration modules, and data logging software |
This configuration ensures that our laboratory extruder meets the demands of various research applications, offering high precision, flexibility, and ease of operation.
▏Small-scale extruder Production Process
To ensure consistent experimental results and precise product quality, the production process of our laboratory extruder is carefully designed. The following flow diagram illustrates the entire process from raw material preparation to final output:
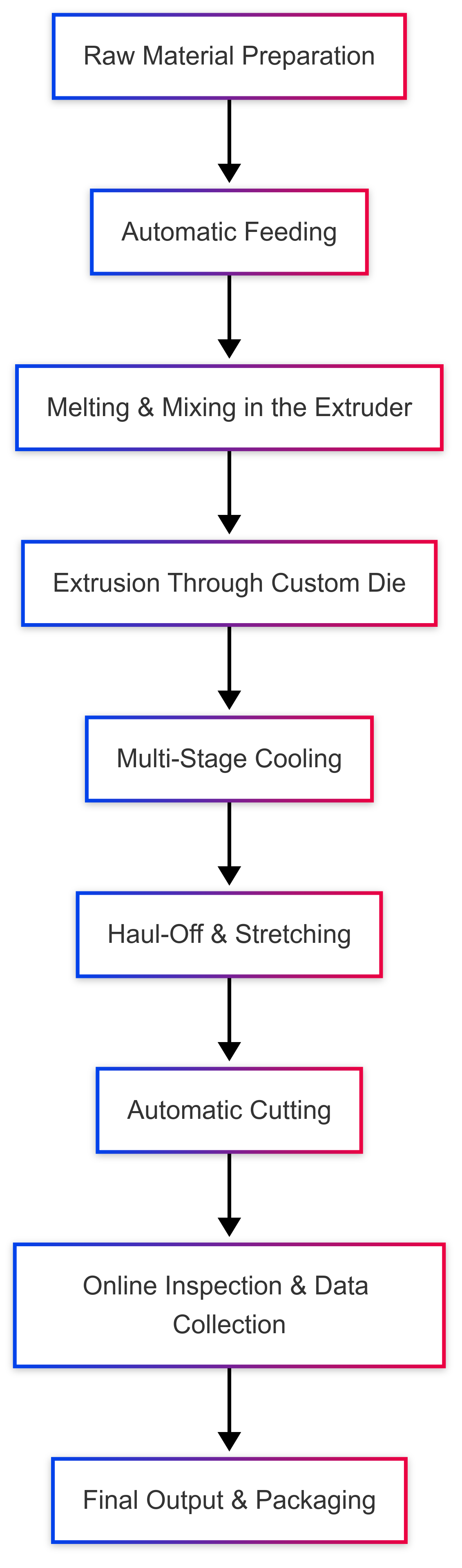
Process Steps Explained
 | Raw Material Preparation Thermoplastic resins, additives, and pigments are accurately weighed and blended. Pre-drying and screening ensure the raw material is free of impurities. |
 | Automatic Feeding |
 | Melting & Mixing The material enters the melting chamber, where the twin-screw system efficiently heats, melts, and homogenizes it. Precise control of temperature and screw speed ensures optimal plasticization. |
 | Extrusion Through Custom Die The molten material is forced through a customized flat die, forming a continuous sheet. Die settings are adjusted to achieve the desired width and initial thickness. |
 | Multi-Stage Cooling The extruded sheet is rapidly cooled through a combination of water and air cooling, solidifying the material uniformly. Controlled cooling minimizes internal stresses and dimensional variations. |
 | Haul-Off & Stretching A servo-controlled haul-off system uniformly pulls the cooled sheet, ensuring consistent stretching and precise thickness. Real-time monitoring of tension ensures that the sheet maintains the ±0.05mm tolerance. |
 | Automatic Cutting The continuous sheet is automatically cut into pre-determined lengths using a high-precision cutter. Automatic length detection ensures smooth, burr-free edges. |
 | Online Inspection & Data Collection High-precision sensors and cameras monitor the sheet’s thickness, width, and surface finish in real time. Data is collected and fed back into the control system for continuous process adjustments. |
 | Final Output & Packaging The approved ABS sheets are coiled, stacked, and packaged automatically for efficient storage and transport. The final product meets all specified quality criteria and is ready for further testing or market release. |
▏Customer Case Studies
 | Case Study 1: American R&D Laboratory
Background: An American research laboratory specializing in advanced polymer studies required a high-precision laboratory extruder to test new material formulations. Their previous equipment was unable to provide consistent data due to fluctuations in process parameters. Results: Enhanced Data Accuracy: The new Laboratory extruder enabled precise control over temperature and flow, yielding consistent data for material performance analysis. Improved Process Efficiency: The automated control system significantly reduced manual adjustments, increasing experimental throughput. Lower Operational Costs: The small-scale, energy-efficient design reduced both material waste and energy consumption. |
 | Case Study 2: European University Research Center
Background: A renowned European university’s materials science department needed a benchtop extruder for teaching and research purposes. The objective was to provide hands-on training in polymer processing while ensuring reliable experimental results. Results: Educational Impact: The Benchtop extruder’s intuitive interface and real-time data collection facilitated effective learning and practical experimentation. Research Advancements: High-precision extrusion enabled consistent, repeatable experiments, leading to several published research papers. Versatility: The extruder proved capable of processing multiple types of thermoplastics, expanding the scope of research projects. |
 | Case Study 3: Asian Startup in Material Innovation
Background: A startup in Asia focused on developing eco-friendly plastic products required a mini extruder machine for pilot production and process optimization. The goal was to test small batches before scaling up to full production. Results: Rapid Prototyping: The Mini extruder machine allowed for quick turnaround on prototypes, reducing time-to-market. Process Optimization: Real-time monitoring and data feedback enabled the startup to fine-tune production parameters, resulting in higher quality and consistency. Cost Savings: The compact design and low energy consumption significantly reduced overall production costs during the pilot phase. |
▏Why Choose Us
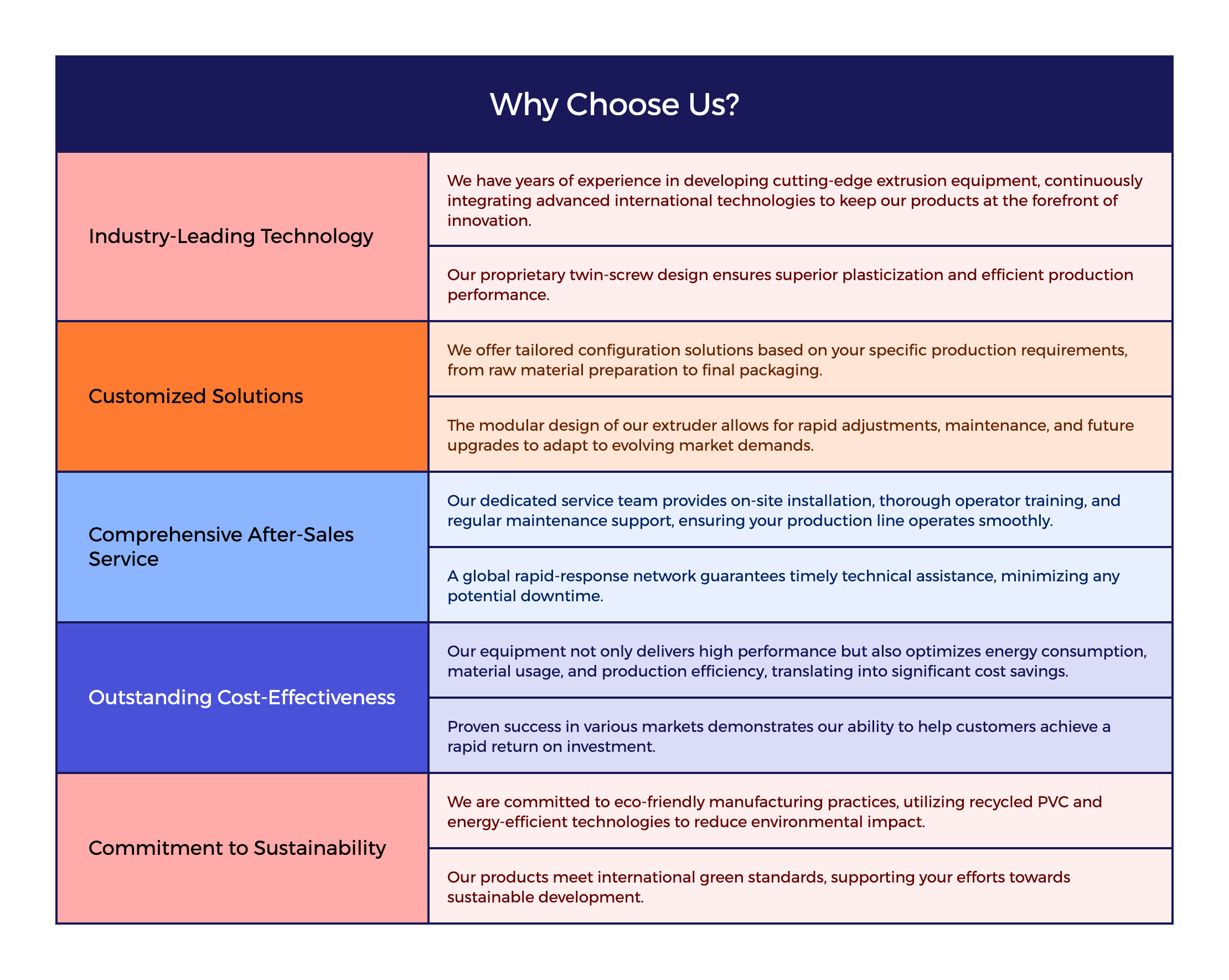
 | Industry-Leading Technology
We possess extensive experience in designing and manufacturing laboratory extruders, continuously incorporating the latest innovations to ensure high precision and reliability. Our proprietary technology ensures that every machine meets stringent quality standards while maintaining excellent operational performance. |
 | Customized Solutions for R&D
We offer tailor-made configurations that suit the specific needs of research institutions, universities, and small-scale manufacturers. Our modular design allows for rapid adjustments and scalability, making it easy to adapt the extruder to different experimental setups. |
 | Comprehensive After-Sales Service
Our service team provides on-site installation, thorough training, and ongoing technical support, ensuring that your extruder operates at peak performance. A global support network and fast response times mean that any issues are addressed promptly, minimizing downtime. |
 | Exceptional Cost-Effectiveness
Our laboratory extruders offer a low initial investment with reduced operating and maintenance costs, making them ideal for research and small-scale production. High production efficiency and minimal waste generation contribute to a rapid return on investment. |
 | Commitment to Sustainability
Designed with energy efficiency in mind, our extruders help reduce carbon emissions and support green manufacturing practices. We promote the use of recycled materials and environmentally friendly processes, aligning with global sustainability goals., |
Achieving high precision in laboratory extrusion is critical for successful material research, process optimization, and pilot production. Our Laboratory extruder – encompassing Small-scale extruder, Benchtop extruder, and Mini extruder machine variants – is engineered to deliver outstanding precision, efficiency, and versatility in a compact, cost-effective package. With advanced temperature control, efficient cooling and calibration systems, and a fully automated control platform, our extruders enable consistent output with a ±0.05mm thickness tolerance, ensuring reliable experimental data and high-quality prototypes.
Whether you are an academic researcher, a materials scientist, or an innovative startup, our laboratory extruder offers a robust solution to meet your R&D needs. With a proven track record in diverse applications and outstanding customer support, we are committed to helping you achieve excellence in material processing and product development.
Contact us today to learn more about our Small-scale extruder and discover how our customized solutions can empower your research and pilot production processes. Let us be your partner in innovation and success!
▏About Us
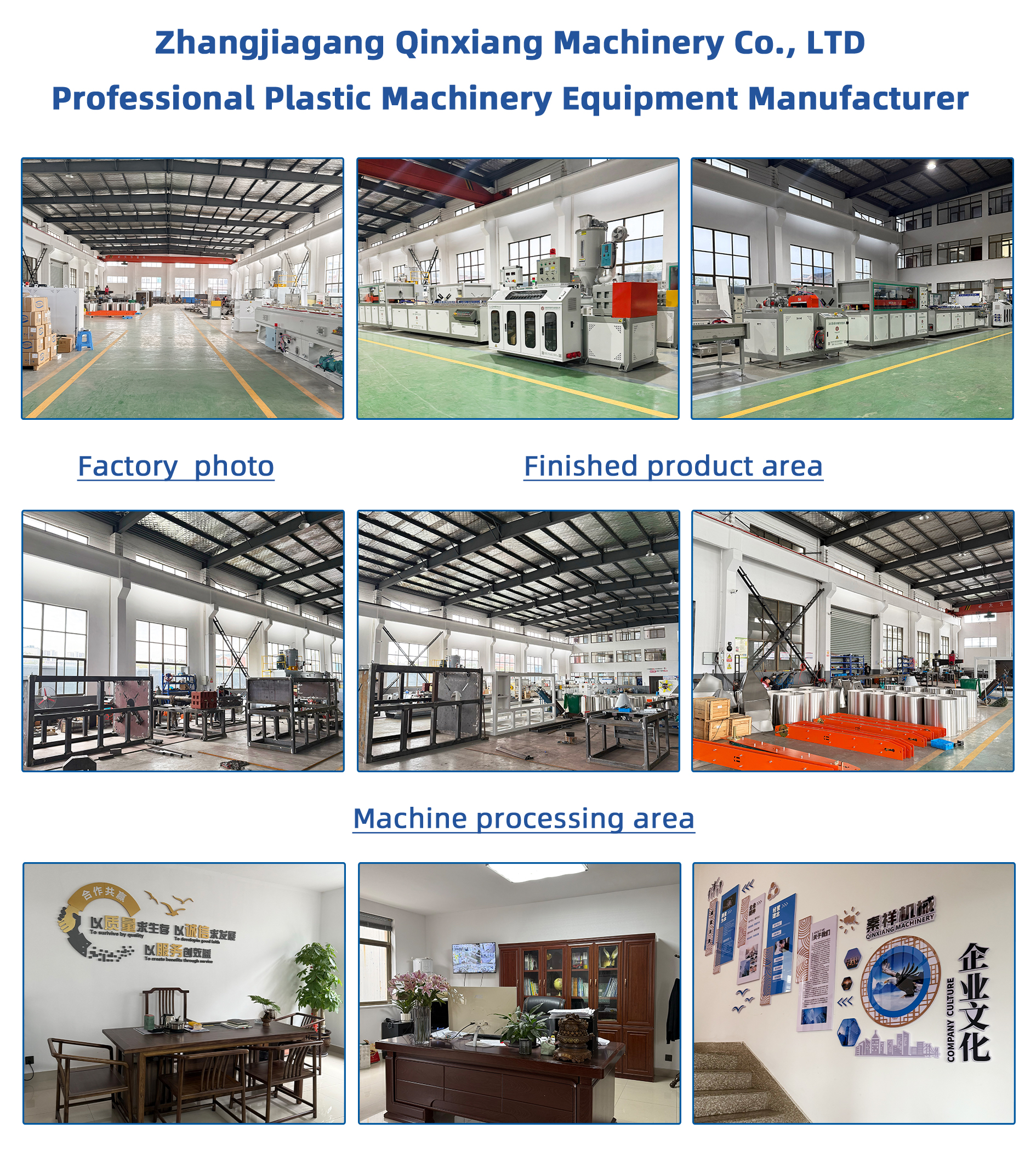
▏Corporate Culture
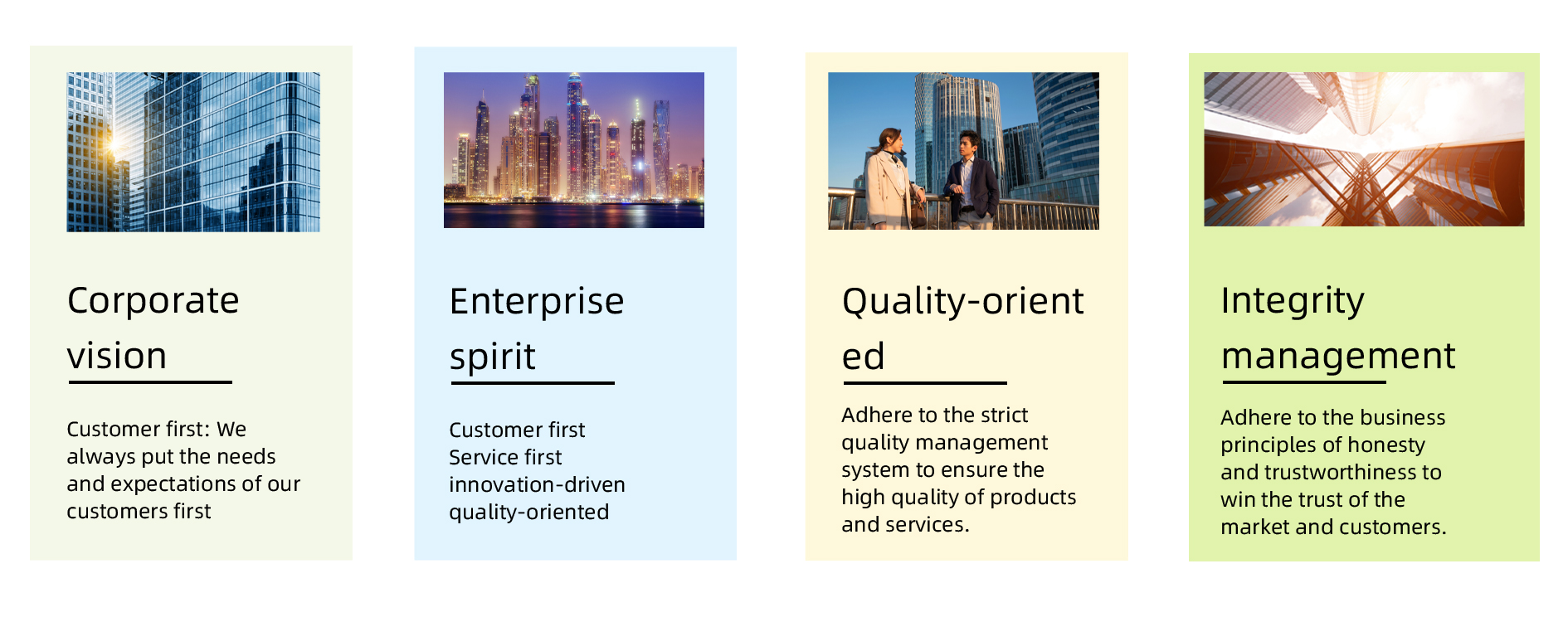
▏Cooperative Parts Supplier
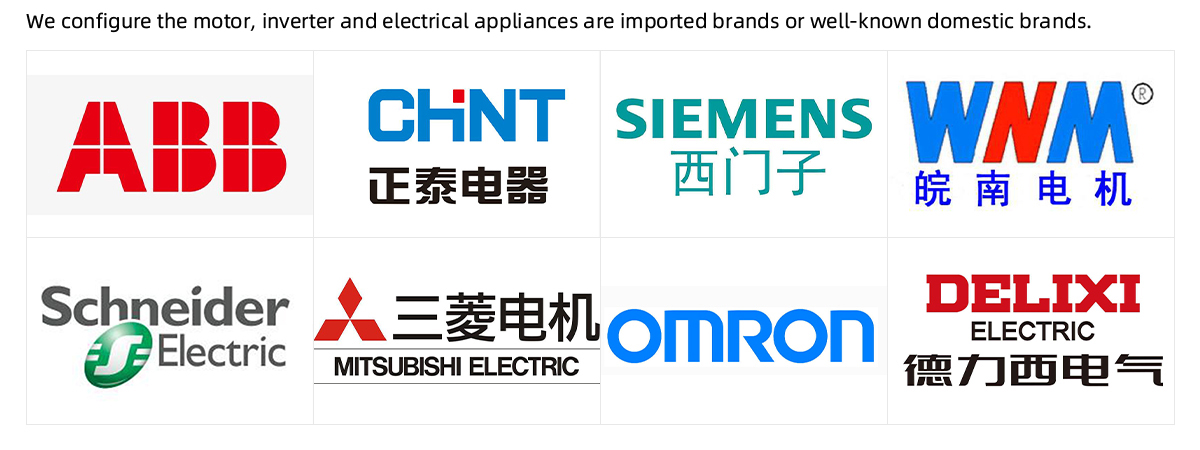
▏Packing And Shipping
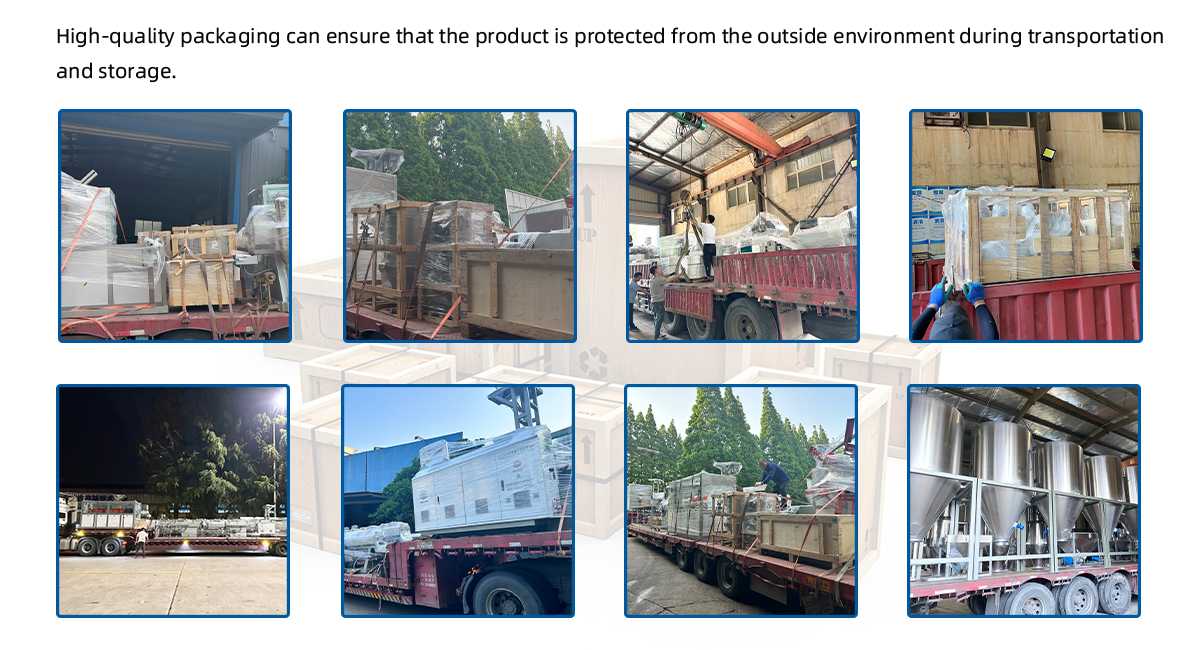